A plasma system’s performance is intrinsically linked to the quality and maintenance of its consumable parts, which play a pivotal role in achieving exceptional cut quality. While regular replacement of consumables can lead to superior results, premature changes can incur unnecessary costs, highlighting the importance of strategic maintenance. Therefore, a comprehensive understanding of how consumables function is essential for optimizing their performance and ensuring cost-effectiveness. By educating our clients on the intricacies of consumable management, Victory CNC Plasma Systems is dedicated to enhancing operational efficiency and supporting our customers in maximizing the value of their investments.
TORCH BODY
The torch body serves as the essential component of your torch, maintaining proper alignment of the consumable parts while facilitating the delivery of pre-flow, plasma gas, and shield gas to the consumables.
Additionally, it is responsible for transmitting the cutting current to the electrode. Therefore, maintaining the cleanliness of the torch body is paramount to its longevity and optimal performance. Accumulation of dirt and grease can lead to detrimental effects such as internal arcing, misfires, and ultimately, torch failure.
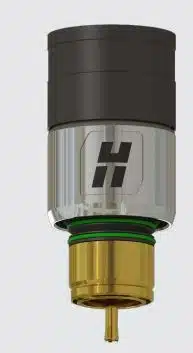
The Electrode
The electrode plays a crucial role in the plasma cutting torch, serving as the primary source of power for the plasma arc, which is essential for achieving precision and reliability in cutting operations. It acts as both the starting point and the electrical contact point for the plasma arc, ensuring seamless initiation and stability during the cutting process. A key feature of the electrode is its plasma arc attachment point, which consists of a small cylindrical insert made from high melting point materials such as tungsten or hafnium. This insert is engineered to endure the extreme temperatures generated by the plasma arc, thereby enhancing the efficiency and longevity of the cutting torch. Understanding the vital function of the electrode can significantly enhance operational performance
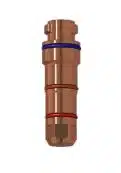
The Nozzle
Maintaining the integrity of your plasma cutting nozzle is crucial for achieving optimal cut quality, as a new nozzle features a perfectly round orifice with sharp inside and outside edges that promote precision. Common issues affecting nozzle performance often stem from an incorrect matchup of consumables. Additionally, factors such as piercing and cutting too close to the workpiece, exceeding the maximum recommended thickness for metal, incorrect gas settings, excessive amperage, using electrodes beyond their lifespan, and improper pierce delays can lead to nozzle damage. To ensure the highest quality cuts, operators should promptly replace nozzles if the orifice exhibits any signs of wear, such as being nicked, notched, out-of-round, or having rounded edges. Victory CNC Plasma Systems strongly recommends replacing nozzles and electrodes as a set to maintain superior cutting performance
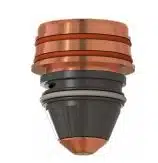
The Swirl Ring
The primary function of the swirl ring is to manage the swirling action of the plasma gas flow surrounding the electrode, which is crucial for achieving optimal cutting results. By centering the cutting arc precisely on the electrode and directing it through the nozzle, the swirl ring enhances the stability and focus of the arc. Furthermore, it constricts the cutting arc, which not only accelerates cutting speeds but also increases the capability to cut through thicker materials. This intricate design feature significantly contributes to the overall efficiency and performance of plasma cutting operations, ensuring that users can achieve the highest quality results in their projects.
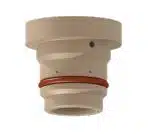
The Shield
The shield plays a critical role in safeguarding the vital components of the plasma cutting system, particularly the nozzle, from molten splatter. It not only cools the nozzle but also significantly contributes to achieving superior cut quality and fast cutting speeds. However, it is important to be aware of potential issues with the shield, such as damage to the main orifice or clogging of the vent holes, as these can adversely affect performance.
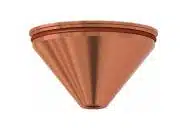
Inner Retaining Cap
Some larger plasma systems, such as HyPerformance® and X-Definition® plasma systems, use an inner retaining cap. The inner retaining cap’s primary function is to hold the nozzle and swirl ring in place while directing coolant flow to the exterior of the nozzle.
The most common feature of the inner retaining cap are the vent holes.
It is essential to keep the threads clean. Dirt or grease on the ring can burn
the cap. Dirt will damage threads over time, requiring the cap to be replaced
prematurely.

Outer Retaining Cap
The outer retaining cap holds the shield in place over the nozzle (or inner retaining cap, if applicable) and directs secondary gas or shield gas to the shield.
This should be inspected where the shield seals to ensure that the threads and o-rings are in good shape. You also need to make sure threads are free of dirt to prevent thread damage.
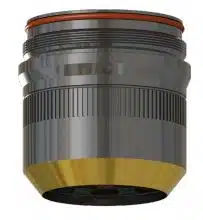
You must be logged in to post a comment.